Electrical Earthing – Components, Methods & Types of Earthing – Electrical Grounding Installation According to NEC and IEC
What is Electrical Earthing or Grounding?
Earthing, also known as Grounding, is the process of connecting electrical systems, equipment, and devices to the ground (the Earth) to ensure safety and proper functionality in electrical installations. Earthing involves establishing a conductive path from the electrical system to the Earth’s conductive surface through grounding electrodes, conductive wires, and grounding conductors.
In other words, connecting the metallic (conductive) parts of an electric appliance or installation to the earth (ground) is known as Grounding or Earthing. The earthing or grounding system involves connecting the metallic components of electric machinery and devices to an earth plate (ground rod) or earth electrode via an earth lead (grounding conductor) buried in moist soil. This connection is established using a thick copper conductor wire with very low resistance for safety reasons.
Earthing, or grounding, is the process of connecting parts of electrical apparatus, such as metallic coverings and the earth terminals of socket cables, as well as stay wires that do not carry current, to the earth. Additionally, earthing involves connecting the neutral point of a power supply system to the earth to minimize the risk of danger during the discharge of electrical energy.
Note: As the terms Earthing and Grounding are used interchangeably, we will use both in the context of NEC and IEC for better understanding. Follow the local area codes such as NEC 250.52(A), 250.53, 250.66 250.122, IEC/BS EN 62561-2 and IEC (62305-3), BS-7671 & associated tables and IEEE standards related to the grounding and earthing)
- For more premium resources, refer to : How to Size the Earth Conductor, Earthing Lead & Earth Electrodes?
Good to Know:
Difference between Earthing, Grounding, and Bonding
While the terms grounding and earthing are interchangeably used to represent the same thing, the term ‘Bonding,’ on the other hand, refers to the practice of joining two wires, conductors, pipes, or appliances together. It also encompasses connecting the metallic parts of different machines, not intended to carry electric current during normal machine operation, to ensure they are at the same electric potential. Let’s distinguish between the terms used as follows:
- Earthing:
In many parts of the world, especially in Europe, Commonwealth and IEC following countries, the term “earthing” is commonly used. Earthing refers to the process of connecting electrical systems and equipment to the ground (the Earth) to ensure safety and functionality. It involves creating a connection between the electrical system and the Earth’s conductive surface through grounding electrodes (such as ground rods or plates) and conductive wires. The primary purpose of earthing is to prevent electric shock, protect against electrical faults, and ensure the stable operation of electrical systems.
- Grounding:
In North America, particularly in the United States, the term “grounding” is often used. Grounding also refers to the same process as earthing but uses different terminology. It involves connecting electrical systems and equipment to the ground to achieve the same safety and operational objectives. Grounding includes establishing a connection to the Earth through grounding conductors, grounding electrodes, and grounding conductive paths.
- Earthing and Grounding:
Earthing and Grounding are essentially the same terms used to describe the process of establishing a connection to the ground. Grounding is the term commonly used for this purpose in North American standards, such as IEEE, NFPA, NEC, ANSI, and UL, while Earthing is the preferred term in European, Commonwealth countries, and British standards, like IS and IEC.
In essence, both earthing and grounding serve the same fundamental purposes in electrical systems.
- Bonding:
The term “Bonding” is used for joining two wires (as well as conductors, pipes, or appliances together). Bonding is known as connecting the metallic parts of different machines, which are not considered to be carrying electric current during normal operation, to bring them to the same level of electric potential.
In the context of the National Electrical Code (NEC), bonding refers to the practice of intentionally creating low-impedance connections between metallic components to ensure electrical continuity and conductivity.
Equipment Bonding Conductor (EBC) and the grounding and bonding of electrical systems, pools and spas, communications systems, and gas piping systems are addressed in NEC Article 250, which provides comprehensive guidelines. These guidelines include requirements for grounding electrode conductors, bonding jumpers, and grounding electrode systems.
Another example of bonding is connecting both the Neutral Bar and the Ground Bar in the main panel via a jumper wire. This connection is not required in the sub-panel, as it is already established in the main service load center.
- Related Post: Difference Between Grounding, Earthing and Bonding
Why is Earthing Important?
The primary purpose of earthing is to avoid or minimize the danger of electrocution, fire due to earth leakage of current through an undesired path, and to ensure that the potential of a current-carrying conductor does not rise with respect to the earth beyond its designed insulation.
When the metallic parts of electrical appliances (parts that can conduct or allow the passage of electric current) come in contact with a live wire, possibly due to installation failure or cable insulation breakdown, the metal becomes charged, accumulating static charge. If a person touches such charged metal, the result is a severe electric shock.
To prevent such instances, power supply systems and parts of appliances need to be earthed, transferring the charge directly to the earth. This is why Electrical Earthing or Grounding is essential in electrical installation systems.
Below are the basic needs of Earthing:
- To protect human lives and ensure the safety of electrical devices and appliances from leakage current.
- To maintain a constant voltage in the healthy phase, particularly in the event of a fault occurring on any one phase.
- To protect electric systems and buildings from lightning.
- To serve as a return conductor in electric traction systems and communication.
- To avoid the risk of fire in electrical installation systems.
Different Terms Used in Electrical Earthing
Earth / Ground: The proper connection between electrical installation systems via a conductor to the buried plate in the earth (earth plate or ground electrode) is known as Earth. The term Ground is used for the same thing in North America (NEC/CNC).
Earthed / Grounded: When an electrical device, appliance, or wiring system is connected to the earth through an earth electrode (ground Rod), it is known as an earthed device or simply “Earthed or Grounded”
Solidly Earthed: When an electric device, appliance, or electrical installation is connected to the earth electrode without a fuse, circuit breaker, or resistance/impedance, it is called “solidly earthed.”
Earth Plate / Ground Electrode: A conductor (such as copper ground rod or conductive earth plate) buried in the earth for the electrical earthing system is known as an Earth Electrode, Ground Electrode of Ground Rod. Earth electrodes come in different shapes such as conductive plates, conductive rods, metal water pipes, or any other conductor with low resistance.
Earthing Lead / Grounding Conductor: The conductor wire or conductive strip connected between the Earth / Ground electrode and the electrical installation system and devices is called the Earthing lead or grounding conductor.
Earth Continuity Conductor: The conductor wire that is connected among different electrical devices and appliances, such as main panels, distribution boards, different plugs, and appliances, is called the earth continuity conductor (grounding electrode conductor in North America). It may be in the shape of a metal pipe (fully or partially), or cable metallic sheath, or flexible wire.
Sub Main Earthing Conductor / EGC: A wire connected between the switchboard and distribution board, i.e., the conductor related to sub-main circuits. It is known as equipment grounding conductor (EGC) in North America.
Earth / Ground Resistance: This is the total resistance between the earth electrode and the earth in Ω (Ohms). Earth resistance is the algebraic sum of the resistances of the earth continuity conductor, earthing lead, earth electrode, and earth. The recommended values of ground resistance is given below in this article.
Points to be Earthed
Earthing is not done arbitrarily. According to NEC (National Electrical Codes) and IEEE (Institute of Electrical and Electronics Engineers) rules and regulations:
- All metal casings or metallic coverings containing or protecting any electric supply line or apparatus, such as GI pipes and conduits enclosing VIR or PVC cables, iron-clad switches, iron-clad distribution fuse boards, etc., should be earthed (connected to the earth).
- The earth pin of 3-pin lighting plugs/outlets, sockets, and 4-pin power plugs/sockets (as well as all other plugs/sockets and outlets/receptacles with a grounding pin) should be efficiently and permanently earthed.
- The frames of every generator, stationary motor, and metallic parts of all transformers used for controlling energy should be earthed by two separate and distinct connections with the earth.
- In a DC 3-wire system, the middle conductors should be earthed at the generating station.
- Stay wires for overhead lines should be connected to the earth by connecting at least one strand to the earth wires.
Related Post: Testing Electrical and Electronics Components and Devices with Multimeter
Components of Earthing / Grounding System
A complete electrical grounding / earthing system consists of the following basic components.
- Earth Continuity Conductor (Grounding Electrode Conductor)
- Earthing Lead (Grounding Conductor)
- Earth Electrode (Earth Plate or Ground Rod)

Earth Continuity Conductor / Earth Wire (Grounding Electrode Conductor)
That part of the earthing system which interconnects all metallic components of an electrical installation – such as conduits, ducts, boxes, metallic shells of switches, distribution boards/main panels, fuses, regulating and controlling devices, and metallic parts of electrical machines like motors, generators, transformers, and the metallic framework where electrical devices and components are installed is known as the earth wire or earth continuity conductor (ECG and Grounding conductors), as shown in the figure above.
The resistance of the earth continuity conductor is very low. According to IEEE rules, the resistance between the consumer earth terminal and the earth continuity conductor (at the end) should not exceed 1Ω. In simple terms, the resistance of the earth wire should be less than 1Ω.
The size of the Earth Continuity Conductor or Earth Wire depends on the cable/wire size used in the wiring circuit.
Size of Earth Continuity Conductor
The cross-sectional area of the circuit protective cable (CPC), also known as the protective conductor, should adhere to Regulations 543.1.3 and 543.1.4 (Regulation 542.3.1 when earth conductor is buried in the ground) and section of Section 544 – IEC Regulation 543.1.1 (Table 43.1 and Tables 54.2 to 54.6, as well as Table 54.7) in BS 7671:2018+A2:2022. The calculation based on reference formula from BS 7454 is also acceptable way to size the protective earth conductor.
The cross-sectional area of the Earth Continuity Conductor should be at least half of the cross-sectional area of the thickest wire used in the electrical wiring installation. The minimum size is 6mm2 and maximum wire size is 25mm2 – (Regulation 543, 544.1.1 of BS 7671 and based on IEC Table 5.1 (especially in case of PNB (Protective Neutral Bonding, also known as TN-C-S PNB) when PME earthing isn’t used)).
The size of PEN conductor and protective earth conductor (also known Circuit Protective Conductor (CPC) in PME Protective Multiple Earthing also known as TN-C-S PME) should be sized according to the Regulations 542.3.1 and Table 54.8 of BS 7671:2018+A2:2022.
According to NEC table 250.122, the minimum wire size for single equipment grounding conductor (EGC) is 4 AWG (21.15 mm2) copper (Section 392.10(B)(1)(c).
According to IEC, the typical size of the bare copper wire used as an earth continuity conductor is 3 SWG (32 mm2).
However, it’s important to note that you shouldn’t use a size less than 14SWG (2.9 mm2) for the earth wire. Copper strip can also be used as an earth continuity conductor instead of bare copper wire, but only if recommended by the manufacturer.
The recommended size of a grounding conductor in the National Electrical Code (NEC) depends on several factors, including the size of the circuit, the type of wiring, and the specific application. The NEC provides tables that specify the minimum size of grounding conductors based on the size of the circuit conductors and the type of raceway or cable used.
For example, in a typical residential wiring scenario, the NEC might specify the minimum size of the ground conductor based on the size of the circuit conductors. Common sizes for residential grounding conductors include #10 AWG or #8 AWG for smaller branch circuits.
Earthing Lead or Earthing Joint
The conductor wire connected between the earth continuity conductor and the earth/ground electrode (such as a copper ground rod) or earth plate is called the earthing joint or ‘Earthing lead.’ The point where the earth continuity conductor and the earth electrode meet is known as the ‘connecting point,’ as shown in the figure above.
The earthing lead is the final part of the earthing system, which is connected to the earth electrode (located underground) through the earth connecting point.
It is advisable to minimize joints in the earthing lead, keeping them smaller in size and straight in direction.
Generally, copper wire can be used as the earthing lead, but copper strip is also employed for high installations as it can handle high fault currents due to its wider area compared to copper wire.
A hard-drawn bare copper wire is also used as an earthing lead. In this method, all earth conductors are connected to one or more common connecting points, and then the earthing lead is used to connect the earth electrode (earth plate) to the connecting point.
To enhance the safety factor of the installation, two copper wires are used as the earthing lead to connect the metallic body of the device to the earth electrode or earth plate. For instance, if two earth electrodes or earth plates are used, there would be four earthing leads. It’s important to note that the two earthing leads are not considered as parallel paths for fault currents but both paths should function properly to carry the fault current, ensuring better safety.
Size of the Earthing Lead
The size or area of the earthing lead should not be less than half of the thickest wire used in the installation.
The recommended size of the earthing lead is #4 AWG or #3 SWG as the largest and not less than #10 AWG or #14 SWG as the minimum. If a wire with dimensions of 37/.083 inches (0.20 inch2 or 129 mm2, nearest metric stranded size 120 mm2) is used, or if the load current is 200 Amps from the supply voltage, it is advisable to use copper strip instead of a double earthing lead. The earth lead connection methods are shown in the figure above.
Earthing / Grounding Electrode (Earth Plate or Ground Rod)
A metallic electrode or plate buried in the earth (underground) serves as the final component of the electrical earthing / grounding system. In simple terms, the ultimate underground metallic plate, connected with the earthing lead, is referred to as an earth plate or earth electrode.
A metallic plate, pipe, or solid copper rod (as ground electrode) can be employed as an earth electrode, offering very low resistance and safely carrying fault current towards the ground (earth).
Size of Earth / Ground Electrode
Both copper and iron can be used as earthing electrode. The size of earth electrode:
- In case of copper
2×2 (two feet wide and two feet in length) with a thickness of 1/8 inch, i.e., 2′ × 2′ × 1/8″ (600 × 600 × 3 mm).
- In case of Iron
2′ × 2′ × ¼” = 600 × 600 × 6 mm
It is recommended to bury the earth electrode in moist soil. If this is not possible, then add water to the GI (Galvanized Iron) pipe to create the necessary moisture conditions. That’s why salt and charcoal are added in the earthing pit for grounding.
The size of ground rod
in case of solid copper:
- Height = 8 feet (≈2.5 meters)
- Diameter = ½ inches (12 mm)
In case of galvanized steel and hollow sections of GI:
- Height = 0.63 inches (16 mm)
- Diameter = ≈1 inch (25 mm)
In the earthing system, place the earth electrode in a vertical position underground, as shown in the figure above. Additionally, surround the earth plate (please note that the earth electrode and earth plate are the same) with a 1-foot (about 30 cm) layer of powdered charcoal and lime mixture. A ratio of 1:3 e.g. 1kg of Salt + 3 kg of charcoal) is good enough for general purpose plate earthing and grounding.
This practice facilitates a potential increase in the size of the earth electrode, ensuring better continuity in the earth (earthing system) and also helps maintain the moisture condition around the earth plate.
Good to Know:
Avoid using coke (the remaining 88% carbon after burning coal in the furnace to emit all the gases and other components) or stone coal instead of charcoal (wood coal) because it can cause corrosion in the earth plate.
Since the water level varies in different areas, the depth for earth electrode installation also differs. However, the depth for earth electrode installation should not be less than 10 feet (3 meters) and should be below 1 foot (304.8 mm) from the constant water level.
Motors, generators, transformers, etc., should be connected to the earth electrode at two different places.
Related Post:
- Why is Copper Rod Used as Ground Rod in Grounding / Earthing System?
- Why is the Grounding Wire Bare and Not Insulated?
Earth Plate or Earth Electrode Size for Small Installation
In small installations, use a metallic rod with a diameter of 25mm (1 inch) and a length of 2m (6ft) instead of an earth plate for the earthing system. The metallic pipe should be buried 2 meters below the surface of the ground. To maintain the moisture condition, surround the earth plate with a 25mm (1 inch) mixture of coal and lime.
For effectiveness and convenience, you may also use copper rods with diameters ranging from 12.5mm (0.5 inches) to 25mm (1 inch) and a length of 4m (12ft). The installation method with more details for rod earthing is explained below in this article.
Earth / Grounding Resistance
The ground resistance depends on multiple factors such as the length and depth of the ground electrode or plate, diameter of the ground rod, number of ground electrodes, type of grounding and earthing system, and the associated soil and environment.
Ground Resistance According to NEC
- According to NEC 250.56, the recommended grounding resistance should be less than 25 ohms, and for sensitive applications like ICU units in hospitals, a maximum resistance of 50 ohms is allowed. An additional ground rod should be installed if the impedance exceeds 50 Ω.
Ground Resistance According to IEEE and NFPA
- According to IEEE and NFPA standards, the recommended Ground resistance for earthing and bonding in telecommunications applications is typically less than 5 ohms.
Earth Resistance According to IEC
- According to the IEC, the ideal value of earth resistance should be between 1-10Ω. (See IEC/BS EN 62561-2:2012)
If ground resistance exceeds the recommended level, follow the steps below to address the issue:
- Perform soil treatment for conductivity according to IEEE 80-2013 (clause 14.5 (a), (b), (c), (d))
- Increase the diameter of the ground electrode
- Increase the number of grounding rods (using supplementary ground rods mention in 250.4(A)(5), 250.4(B)(4), and 250.54.)
- putting salt and charcoal in earth-pit to decrease the resistance to the suitable value.
Methods and Types of Electrical Earthing / Grounding
Grounding / Earthing can be achieved through various methods. The following discussion covers the different methods employed in earthing, whether in house wiring or in factories and other connected electrical equipment and machines.
Plate Earthing:
In the plate earthing system, a plate made of either copper with dimensions 60cm × 60cm × 3.18mm (i.e., 2ft × 2ft × 1/8 in) or galvanized iron (GI) with dimensions 60cm × 60cm × 6.35 mm (2ft × 2ft × ¼ in) is vertically buried in the earth (earth pit), and it should not be less than 3m (10ft) from the ground level.
To ensure a proper earthing system, follow the steps mentioned in the Earth Plate introduction to maintain the moisture condition around the earth electrode or earth plate.
Pipe Earthing:
In this type of earthing system, a galvanized steel and a perforated pipe of approved length and diameter are placed vertically in wet soil. This is the most common earthing system.
The size of the pipe used depends on the magnitude of the current and the type of soil. The standard dimensions for the pipe are usually 40mm (1.5in) in diameter and 2.75m (9ft) in length for ordinary soil, or greater for dry and rocky soil. The moisture content of the soil determines the length of the pipe to be buried, but typically, it should be 4.75m (15.5ft).
Rod Earthing
Grounding Rod or Ground Electrode earthing is the same method as pipe earthing. A copper rod with a diameter of 12.5mm (1/2 inch), or a galvanized steel rod with a diameter of 16mm (0.6in), or a hollow section of a 25mm (1inch) GI pipe with a length above 2.5m (8.2 ft) is buried upright in the earth either manually or with the help of a pneumatic hammer. The length of the embedded electrodes in the soil reduces earth resistance to a desired value.
A supplementary ground rod should be installed 6 feet (1.8 m) apart if the ground resistance exceeds 25 ohms (specified in NEC Section 250.56).
The exact sizes of the ground rod are mentioned in the above section of this article for “sizing the ground electrode”.
For more details and installation process of Ground Rod, see the article “What is Ground Rod and What does it Do? How to Install a Ground Electrode?“
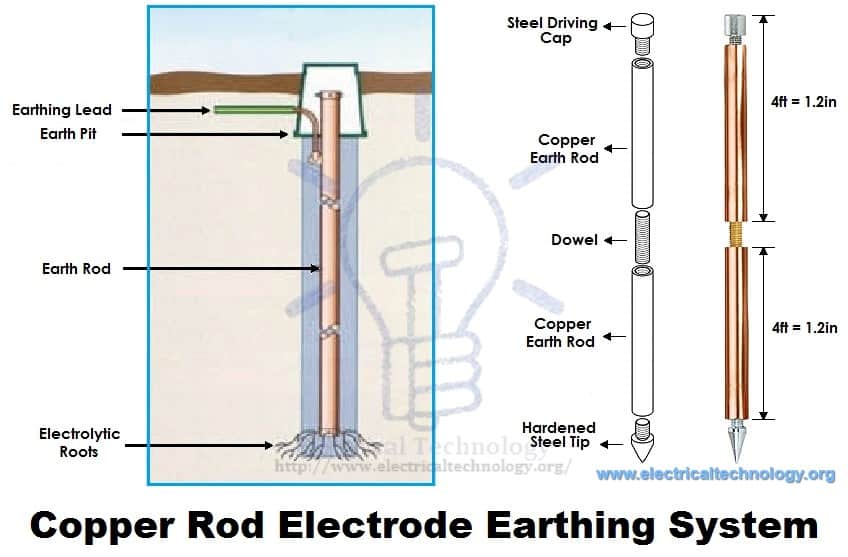
Earthing through the Waterman
In this method of earthing, Galvanized GI pipes are utilized for earthing purposes. Ensure to check the resistance of GI pipes and use earthing clamps to minimize resistance for a proper earthing connection.
If a stranded conductor is used as an earth wire, clean the ends of the wire strands, and ensure they are straight and parallel before securely connecting them to the waterman pipe.
Strip or Wire Earthing:
In this method of earthing, strip electrodes with a cross-section not less than 25mm × 1.6mm (1in × 0.06in) are buried in horizontal trenches with a minimum depth of 0.5m. If copper with a cross-section of 25mm × 4mm (1in × 0.15in) is used, the dimension is 3.0mm2, whether it’s galvanized iron or steel.
If round conductors are used, their cross-sectional area should not be too small, for example, less than 6.0mm2 if it’s galvanized iron or steel. The length of the conductor buried in the ground should provide sufficient earth resistance, and this length should not be less than 15m.
General Method of Electrical Grounding / Earthing Installation
The standard step by step procedure for earthing electric equipment, devices, and appliances is as follows:
- Begin by digging a pit approximately 5 × 5 ft (1.5 × 1.5m) in size, with a depth of 20-30ft (6-9 meters) into the ground. (Note that the depth and width depend on the nature and structure of the ground.)
- Vertically bury an appropriate copper plate (usually 2’ × 2’ × 1/8” or 600×600×300 mm) in the pit.
- Attach 3/4 AWG/SWG earth leads (ground conductor) through nut bolts from two different places on the earth plate.
- Use two earth leads for each earth plate (in case of two earth plates) and tighten them securely.
- Apply grease around the joints to protect them from corrosion.
- Gather all the wires in a metallic pipe from the earth electrode(s), ensuring the pipe is 1ft (30cm) above the ground surface.
- To maintain moisture conditions around the earth plate, surround it with a 1ft (30cm) layer of powdered charcoal (powdered wood coal) and lime mixture.
- Use thimbles and nut bolts to tightly connect wires to the bed plates of machines. Each machine should be earthed from two different places, and the minimum distance between two earth electrodes should be 10 ft (3m).
- Ensure that the earth continuity conductor, connected to the body and metallic parts of all installations, is tightly connected to the earth lead. Perform a continuity test to verify continuity.
- Lastly, test the overall earthing system with an earth tester. If everything aligns with the plan, fill the pit with soil. The maximum allowable resistance for earthing is 1Ω. If it exceeds 1 ohm, increase the size (not length) of earth lead and earth continuity conductors. Keep the external ends of the pipes open and periodically add water to maintain the moisture condition around the earth electrode, crucial for a better earthing system.
NEC Specifications of Grounding
The National Electrical Code (NEC) provides specifications for grounding in various sections. Here are some key sections related to grounding in the NEC:
- NEC Article 250 – Grounding and Bonding:
- 250.4 – Grounding Path and Connections: Specifies that the path to ground from circuits, equipment, and grounding electrodes should be permanent and continuous.
- 250.50 – Grounding Electrode System Installation: Provides requirements for the installation of grounding electrode systems, including the types of electrodes and their installation methods.
- 250.52 – Grounding Electrodes: Describes the types of grounding electrodes and their installation requirements.
- NEC Article 250 – Grounding and Bonding (Part II):
- 250.70 – Grounding Conductor Sizing: Specifies the sizing of grounding conductors based on the size of the circuit conductors.
- 250.122 – Size of Equipment Grounding Conductors: Provides the minimum size requirements for equipment grounding conductors.
- NEC Article 250 – Grounding and Bonding (Part III):
- 250.130 – Equipment Grounding Conductor Installation: Outlines the methods and requirements for installing equipment grounding conductors.
- 250.136 – Equipment Grounding Conductor Material: Specifies the materials that can be used for equipment grounding conductors.
- NEC Article 250 – Grounding and Bonding (Part V):
- 250.164 – Protection of Grounding Conductors: Provides requirements for protecting grounding conductors against physical damage.
- NEC Article 250 – Grounding and Bonding (Part VII):
- 250.210 – Grounding of Equipment: Outlines the requirements for grounding non-current-carrying metal parts of equipment.
SI Specification for Earthing
Various specifications regarding earthing, as recommended by Indian Standards, are provided below:
- An earthing electrode should be positioned (installed) at a distance of at least 1.5m away from the building whose installation system is being earthed.
- The earth resistance should be low enough to enable sufficient current flow to operate protective relays or blow fuses. Its value is not constant as it varies with weather due to dependence on moisture (but should not be less than 1 Ohm).
- The earth wire and earth electrode should be made of the same material.
- The earthing electrode should always be placed in a vertical position inside the earth or pit to be in contact with all the different earth layers.
Related Posts:
- Single Phase Electrical Wiring Installation in Home – NEC & IEC
- Three Phase Electrical Wiring Installation in Home – NEC & IEC
Dangers of Not Earthing a Supply System
As emphasized earlier, earthing is provided for several crucial reasons:
- To avoid electric shock:
- This is a primary purpose of earthing. By connecting the electrical system to the ground, the risk of electric shock is significantly reduced.
- To avoid the risk of fire:
- Earth leakage current, if not properly grounded, can follow unintended paths and lead to the risk of fire. Proper earthing helps direct such currents safely to the ground.
- To ensure that no current-carrying conductor rises to a potential with respect to the general mass of earth beyond its designed insulation:
- Maintaining the designed insulation of conductors is critical. Earthing prevents conductors from reaching potentials that could compromise their insulation and safety.
However, if excessive current is not earthed, appliances may be damaged without the protection of a fuse. It is important to note that excessive currents are grounded at generating stations, minimizing the current carried by earth wires. Therefore, it may not be necessary to earth individual wires (live, earth, and neutral) contained in a PVC. Earthing the live wire can have catastrophic consequences.
I witnessed a tragic incident where a person lost their life due to a live wire getting cut from an overhead pole and falling to the wet ground. Excessive current is typically grounded at generating stations, and if there is a fault in the earthing system, earth fault interrupters provide additional protection. Fuses play a role when the power transmitted exceeds the rating of our appliances, preventing the current from reaching the appliances and safeguarding them by blowing off in the process.
In electrical appliances, if excessive currents are not earthed, users may experience severe shocks. Earthing in appliances becomes active only when there is a problem, serving as a safety measure. In the event of a fault, such as direct contact between a live wire and a metallic part of an electrical appliance, the metal becomes charged, accumulating static charge. Earthing ensures that this charge is transferred to the ground, protecting users from potential shocks.
Moreover, if a live wire accidentally touches the metallic part of a machine in a faulty system, and an individual touches that metallic part, the current flows through their body to the ground, leading to electric shock or even serious injuries and death. This underscores the critical importance of proper earthing practices.
Electrical Grounding & Earthing… To be continued…
Please subscribe below if you want to receive upcoming posts about Earthing/Grounding, covering topics such as:
- Calculating the size of Earth Continuity Conductor, Earthing Lead & Earth Electrodes for different electrical devices and equipment like motors, transformers, home wiring, etc., through simple calculations.
- Understanding Earthing Circuit and Earth Fault Current.
- Protection of the Earthing System and additional devices used in the Earthing/Grounding System.
- Important points to remember when providing Grounding/Earthing.
- Key instructions for a proper earthing system.
- Electricity rules regarding Earthing.
- How to test Earth Resistance using an Earth Tester.
- How to test Earth Loop Resistance using an Ammeter & Voltmeter.
- Protective Multiple Earthing.
- And much more…
Stay tuned for valuable insights into Earthing and Grounding practices in upcoming posts. Subscribe now for regular updates!
Related Posts:
- How to Find the Size of Earth Conductor, Earthing Lead & Earth Electrodes?
- Difference Between Grounding, Earthing and Bonding
- What is the Difference Between Neutral, Ground and Earth?
- Design of Grounding / Earthing System in a Substation Grid
- Difference Between Real Ground and Virtual Ground
- What is the Difference Between Neutral, Ground and Earth?
- Why are Salt and Charcoal Added in Earthing Pit for Grounding?
- Why are Overhead Power Transmission Lines Not Insulated?
- Why is the Ground Wire always Above the Overhead Power Lines?
- What is the Purpose of Ground Wire in Overhead Transmission Lines?